Merck – A WinGuard Success Story
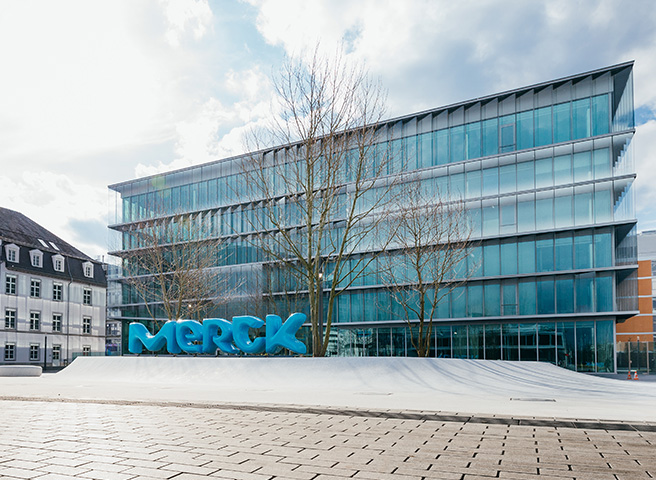
Merck
The Challenge – Holistic safety in the chemical industry
Merck, a leading science and technology company, is active in the areas of Life Science, Healthcare and Electronics. Around 63,000 employees work to make a difference in the lives of millions of people every day for a brighter future: From products and services to develop and manufacture medicines faster, to discovering unique ways to treat diseases, to delivering applications for smart devices, Merck is everywhere. Scientific research and responsible entrepreneurship are critical to Merck’s technological and scientific progress. This principle has applied since the company was founded in 1668, and the founding family is still the majority owner of the listed company.
At Merck, as in many other companies, the digitalization of processes is a constant challenge that affects all areas. A cross-divisional, specialized IT team for security and emergency management takes care of Merck’s own network, which is shielded from external influences by a firewall. The systems must run with maximum availability at all times, as business critical functions must be guaranteed without interruption. In contrast to the entire Group IT, however, it is not possible to rely on outsourcing responsibilities in all areas.
This is because security requirements are not met with standard software, but largely have to be met with specialized and sometimes individual and specific plant software, for example in fi re protection or the command and control systems for the plant fi re department. In the area of hazard management, on the other hand, Merck successfully relies on the open integration platform WinGuard from Advancis. After an intensive project lead time and the development of a new security concept, the existing hazard management system, which no longer met the requirements, was seamlessly replaced.
The scope
- 36 WinGuard operating stations
- 100,000 data points
- 16 adapters
- 2 locations with more than 400 buildings
- CAD Support Plus
- Hot Standby
- Operational control system integration
- User Management Plus
- Switching operations
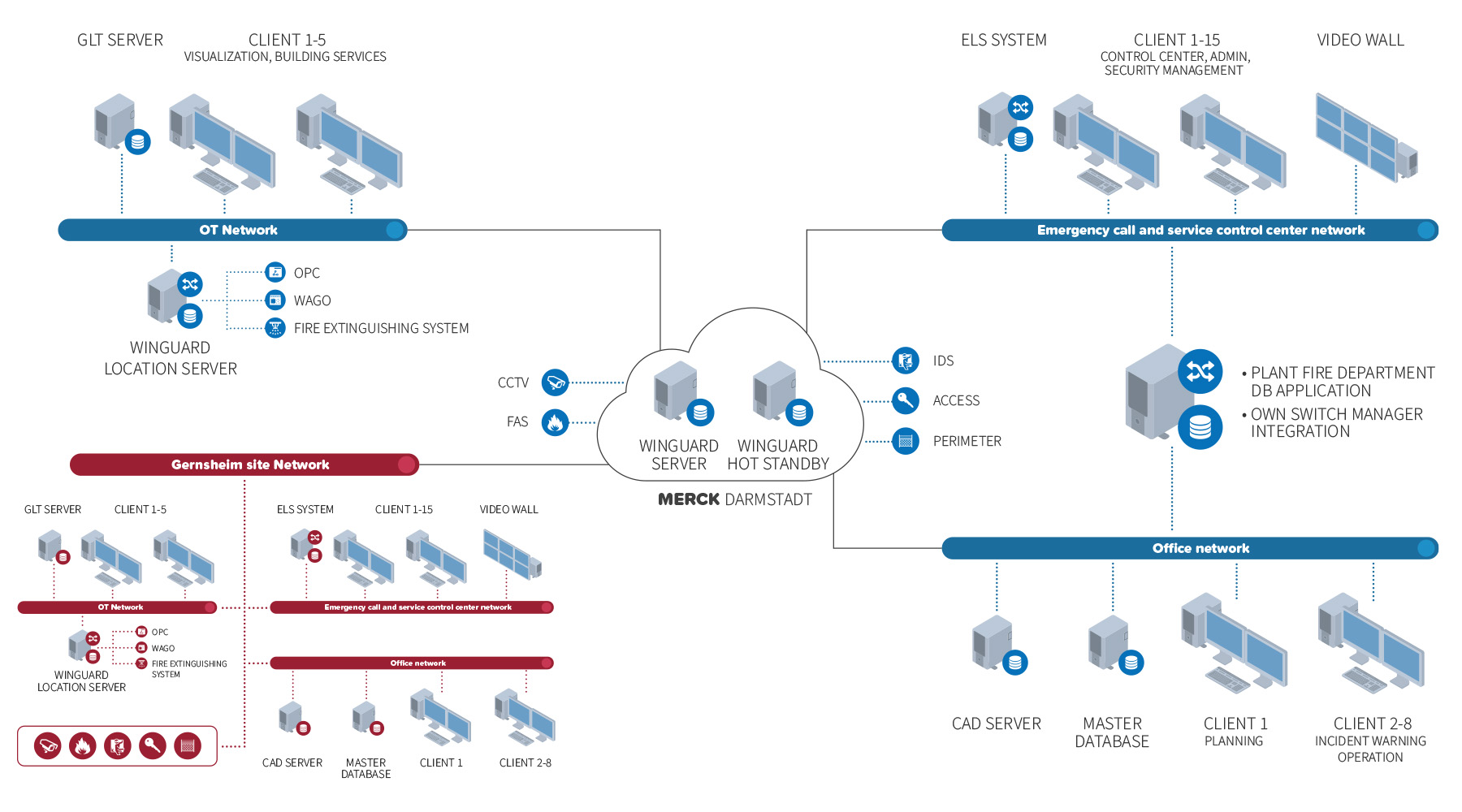
The system concept
With the introduction of WinGuard, Merck has achieved a remarkable transformation and optimization of various processes. The entire process, from detector planning, commissioning and maintenance to deactivation, was successfully digitalized. The comparison with the systems and databases involved was automated as far as possible, while the dual control principle was deliberately applied at certain points to ensure additional security.
WinGuard enabled existing processes to be digitized and thus considerably shortened, accelerated and in some cases completely replaced. This not only led to a significant reduction in errors, but also to a meaningful reduction in manual effort. The reliable display of the current status of the connected plants and systems provides those responsible for safety at Merck with comprehensive situational awareness. This enables them to maintain an overview and to initiate and efficiently process predefined measures in a targeted manner.
A central requirement that WinGuard fulfills perfectly is ensuring data consistency. The central management system prevents data discrepancies and enables users to maintain the data. This ensures that all relevant information is always up-to-date and fully available when required.
Another significant advantage of WinGuard is the promotion of cross-team collaboration. For example, messages from the technical department, which is responsible for system support, can be seamlessly transferred to the fire department. This smooth communication and coordination between departments significantly increases the efficiency and responsiveness of the entire team. Overall, WinGuard has created significant added value by optimizing processes, improving collaboration and ensuring data integrity. Those responsible at Merck are extremely satisfied with the results and continue to see great potential for future improvements.
The advantages
- As a vendor-neutral platform, WinGuard integrates all existing security, building and information technology systems
- Visualization of event messages and procedural instructions for resolving the situation and initiating measures
- Automation of detector switch-offs and switch-ons as well as planning of maintenance appointments using a switching manager for building managers
- Comprehensive autonomous site solutions via location and interface servers
- Redundancy concepts to ensure the high availability of the system
- Message transfers to the plant fire brigade’s operations control system
- Organizational integration into comprehensive safety concepts
- Standardized, user-friendly display and operation of all technical systems
- Seamless documentation of all safety relevant processes
- Automation of the data supply: CAD plans are loaded centrally from a master database so that up-to-date graphics, locations and additional information are always used as the basis for the message display.
- Ensuring the EMA is armed: Automatic actions are used to ensure that security areas are actually armed and a message is generated if there is a deviation from the specification.
Central Security Management
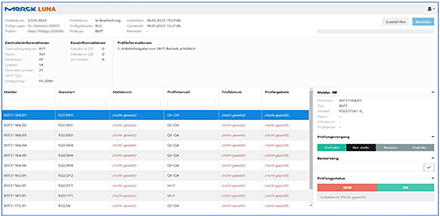
WinGuard visualizes Content and Fault Messages depending on the Situation
The existing web application already supports users in the processing of their daily tasks. The web application was adapted by Merck so that it transmits the desired switching orders to WinGuard and monitors compliance with the target states. The user is notified in WinGuard if there is a deviation from a target status. Particular attention is paid to the use of the authorization definition from the existing web application, which is used as a basis to ensure that only authorized persons can manage switching orders for the defined area of responsibility when a switching order is created.
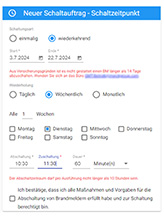
Efficient routine checks thanks to automated switching and mobile app
Routine tests can now be carried out without a monitoring center and the required switching operations can be performed automatically. The inspector receives feedback from the system via a mobile app. This enables considerable savings to be made when carrying out regular detector tests and also enables a one-man inspection process for route card testing.
More Success Stories

Infineon
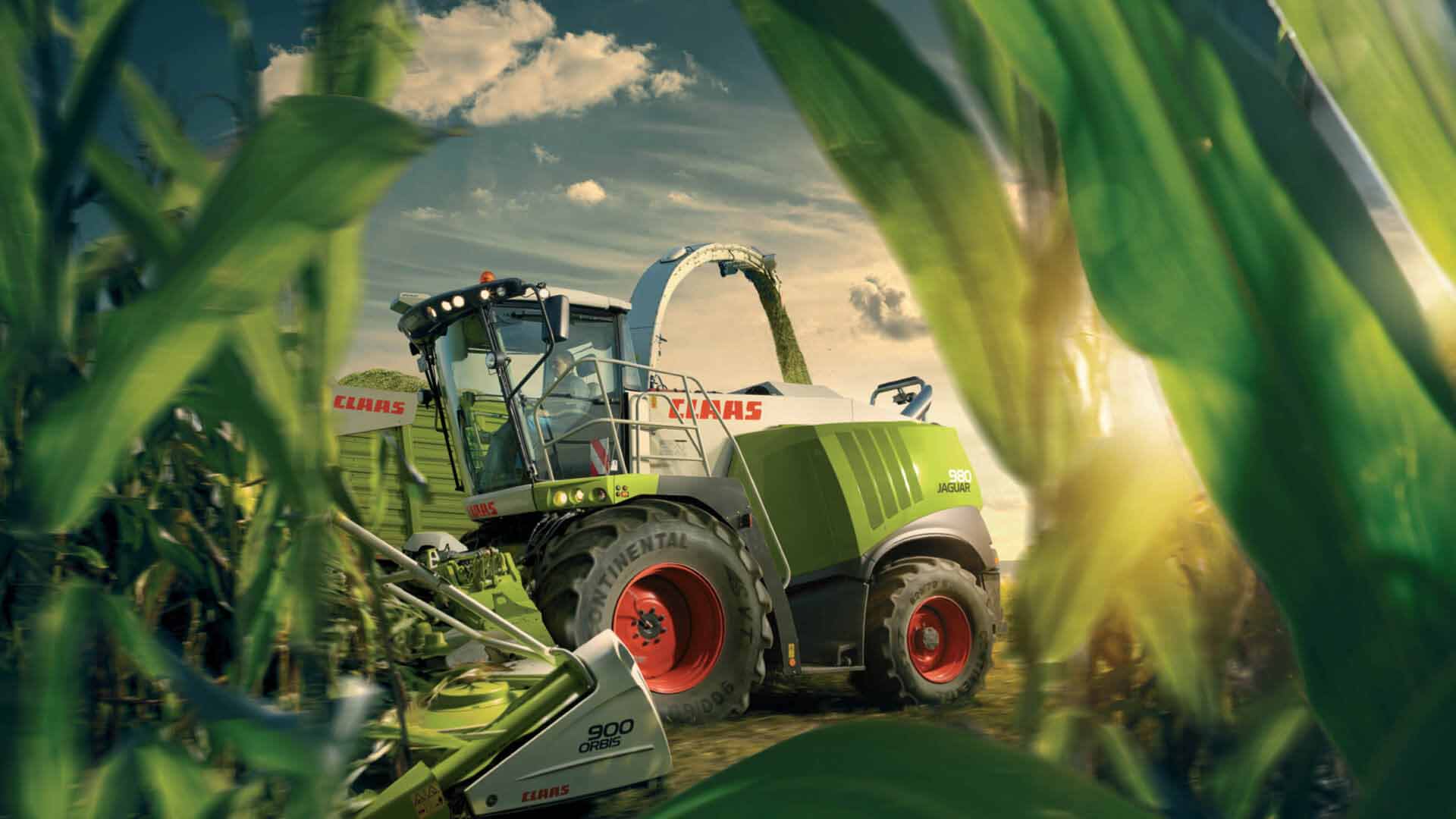
Claas
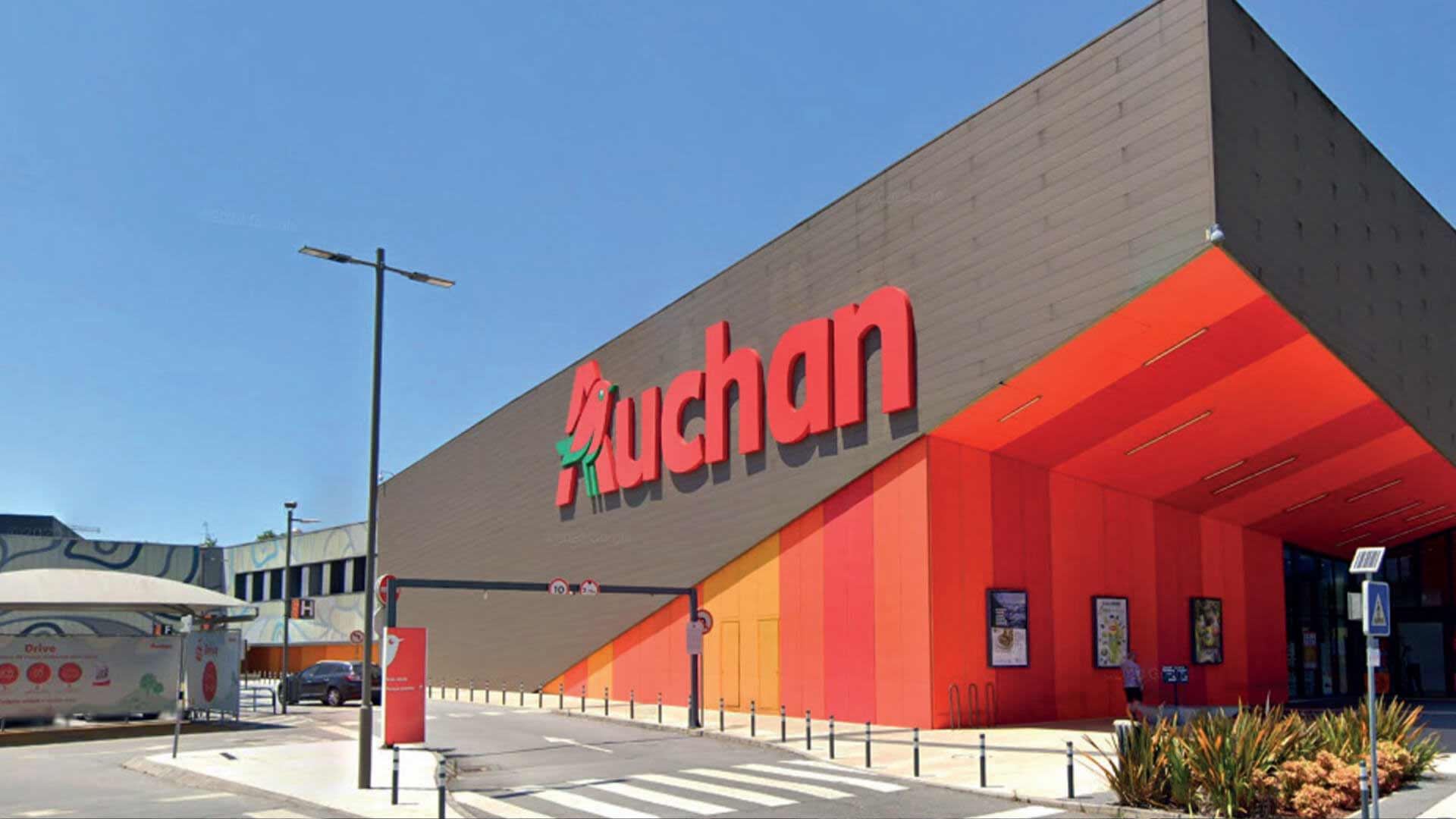
Auchan
You have questions? We are here for you!
Call us and talk to our experts.
If you have any technical problems, our support team will be happy to help you.